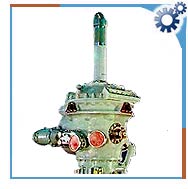
This gearbox comprises a two-stage transmission with an overall reduction of 17.44:1. A normalized energy metric is used to classify seeded faults of the main transmission. Loaded gearbox test runs are used to evaluate the sensitivity of a non-stationary fault detection and classification. The non-stationary fault metric consists of a simple normalized energy index developed to account for a redistribution of side band energy of the dominant mesh frequency and its harmonics in the presence of actual gearbox faults. This index is used to qualitatively assess the presence, type and location of faults. With gearboxes for the main rota and tail rota and no forced air cooling, helicopters have a unique requirement for gearbox oil cooling systems.
The forces acting on a aviation gearbox during flight are simulated on the test stand by means of mechanical load systems. Quality assessment is based on measurement and documentation of all simulated operating conditions, which include speeds, torque, rotor thrust, rotor mast bending, wear, heat balance, vibrations, and oil pressures and oil flow.
A magnesium alloy is used for many navy helicopter gearbox and main transmission housings.